Modern safety and security systems not only protect the operator from the machine but also the machine from human fallibility. Non-tamper-proof access control systems are still causing costly accidents and plant downtimes. Volkswagen Group Components has streamlined the processes in its foundry using the transponder-based Electronic-Key-System EKS from EUCHNER. Access rights to operate robots are now clear and fail-safe. The automotive group is now also able to record relevant process parameters and document all events for enhanced productivity and process reliability.
Murphy’s law states that anything that can go wrong will go wrong, and anybody who operates and maintains machines on a daily basis can confirm this adage. This applies to safety too. Although plant operators generally no longer have to worry about physical harm to themselves thanks to the Machinery Directive (safety), machines still have to be protected from human shortcomings, tampering and malicious attacks (security). Integrated safety and security solutions ensure that machines and installations can operate productively, free from malfunctions and failures.
Volkswagen Group Components in Hanover manufactures mainly chassis and engine components. Various conveyor sections transport components from the casting machine to a machining center, from there to an X-ray quality testing station and then into special carriers at the end of the production line for onward transport to the assembly line. Kuka robots, separated from the workers by protective enclosures, handle the workpieces at the transfer points along the widely branching installation. This takes place fully automatically and generally without incidents. Manual intervention is needed only in the event of faults or for maintenance or setup work.
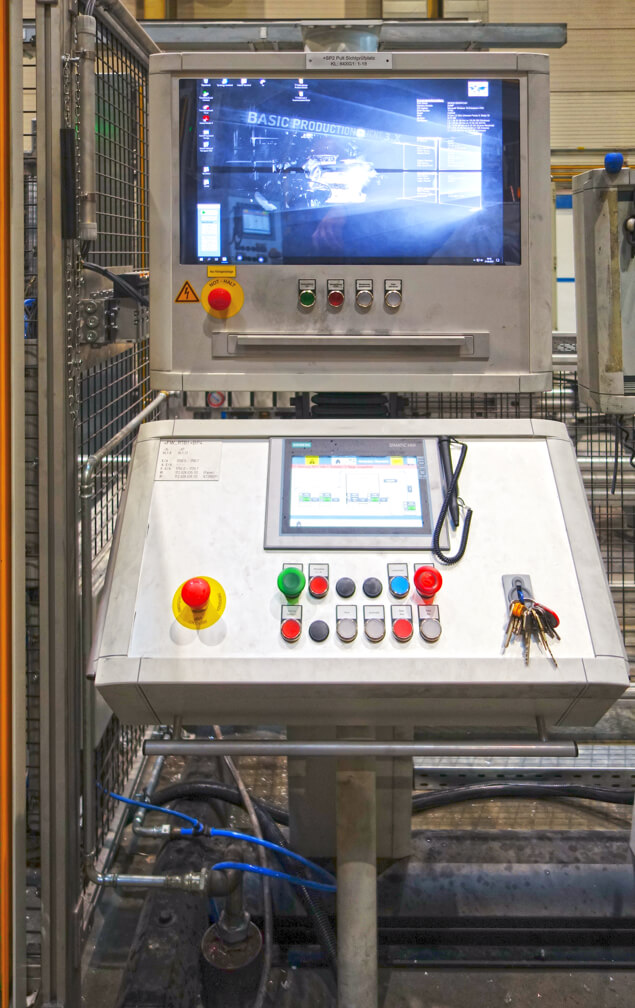
Until 2020, employees could access the robots in the foundry simply by switching between two manual operating modes on the control panel. This enabled appropriately qualified employees to gain access for maintenance, setup or programming work in line with their authorization and skills while the robots were operating at a safety limited speed. So far so good, but the inherent drawbacks of this method cannot be discounted. The weaknesses of password-based systems are well known: they encourage misuse in practice and generally do not meet the required safety standards. Improper operation by inadequately qualified personnel often leads to accidents and plant down- times that impact productivity. Stress, high production targets, the absence of an authorized colleague and frequent personnel changes in daily operations can tempt a well-intentioned but inadequately skilled employee to take matters into their own hands in an emergency.
“We wanted to enhance safety and productivity in our foundry processes and minimize downtimes due to improper operation. This involved fundamentally modernizing the access control system,” explains Heiko Tegtmeier, responsible for electrical planning in the foundry. Only a personalized read/write system with individually preset parameters can guarantee effective security to prevent unauthorized access and tampering. Volkswagen has been relying on EUCHNER’s expertise for almost 20 years. EUCHNER GmbH + Co. KG in Leinfelden is an international, family-owned company with 18 subsidiaries and employs more than 900 people world- wide. Safety engineering, operating systems, switchgear and safety services from EUCHNER ensure safe and reliable operation of machines and installations throughout the Volkswagen Group.
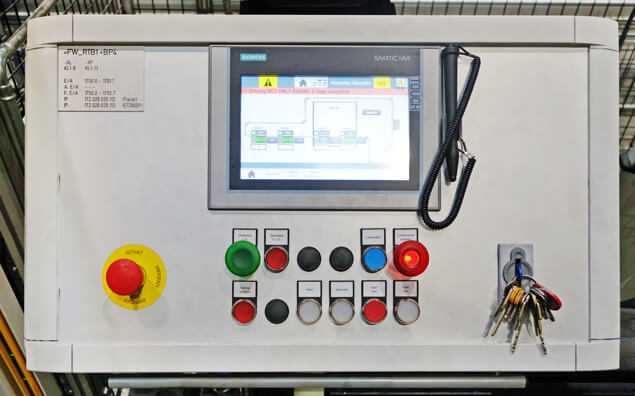
“It really helped that our transponder-based Electronic-Key- System has been successfully applied in other production areas for many years,” says Armin Frerichs, Key Account Manager Automotive at EUCHNER. “This RFID-based read/write system provides electronic access control and management in almost all industrial sectors. The Electronic-Key with integral information memory is what makes the Electronic-Key-System far superior to password-based systems. As an open, freely configurable system with various data interfaces, the EKS is suitable for virtually all applications.”
To operate a machine, the customizable Electronic-Key is inserted into the Electronic-Key adapter near the control panel and held in place by a sturdy spring clip. Power is supplied to the transponder and data are transferred without contact between the Electronic-Key adapter and the Electronic-Key. “Besides reliability and custom programmability, a robust de- sign suitable for tough ambient conditions in a foundry was the key criterion for our decision,” emphasizes Maik Thürnau, Technical Maintenance Manager. This was not the only reason a proprietary alternative solution with USB stick did not make the cut.
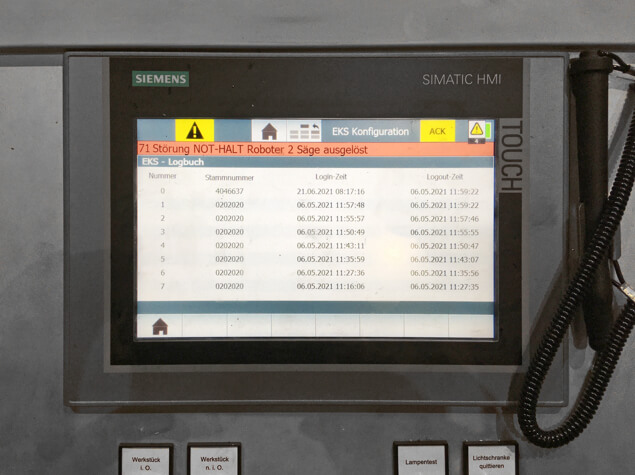
EUCHNER’s versatile Electronic-Key-System EKS now unmistakably defines who may do what where and when at Volkswagen Group Components: each electronically assigned Electronic-Key bears the holder’s individual code containing the defined entry, access and task authorizations at the control system level. Inserting the Electronic-Key to access the ma- chine identifies the Electronic-Key holder and activates their individual user rights. A black Electronic-Key identifies the holder as a machine operator who may perform only tasks related to machine operation. The holder of a green Electronic-Key is recognized as a machine setter or programmer who, by virtue of their training and expertise, is authorized to change pro- cess-relevant machine parameters and perform preparations for the production process. If a user holds a red Electronic-Key, they are authorized to operate all robot functions and change all parameters based on their verified expertise.
Personalized transponder-based Electronic-Keys practically rule out improper operation and tampering. Plant owners benefit from maximum flexibility: They define the data structure on the Electronic-Key and how to interpret it. “We use the innovative EKS system from EUCHNER for more than just controlling machine functions: All process parameters are saved at the control-system level, which also means that all events are retraceable. If necessary, we can use the EKS logbooks and the Electronic-Key’s serial number to find out who did what where and for how long,” adds Tegtmeier. The Electronic-Key-Manager EKM software developed by EUCHNER is used to program the EKS Electronic-Keys and write data to them from a PC.
Installing the Electronic-Key-System EKS from EUCHNER has enhanced the safety of robot operation at Volkswagen Group Components in Hanover: Workers with any access rights can be certain that the robot will not pose a danger to them. Practically ruling out improper operation and tampering has rendered damage and failures due to accidents a thing of the past. “This made the entire installation more reliable and ultimately boosted its productivity. Once again, EUCHNER impressed us as a solution-oriented, constructive and depend- able partner we will gladly continue working with in the future,” summarizes Tegtmeier.